top of page

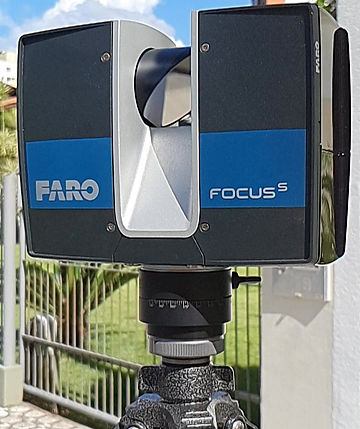
LASER SCANNER 3D
Advanced and modern methodology
With LiDAR technology, 3D laser scanning captures all surrounding surfaces and generates a 3D digital replica of the structure.
HOW?
As the equipment emits laser beams, the beams find the surfaces and return with information on the position and intensity of the signal. Each point contains XYZ coordinates and the set of these points is what we call the Point Cloud.
WHICH EQUIPMENT IS INDICATED?
There are several devices that perform 3D laser scanning. In general, they vary in:
-
Terrestrial
-
Fixed : they provide greater precision (millimeter) and higher resolution of the point cloud, however they demand more time of collection in the field;
-
Furniture : high speed of capture, but with less precision (centimeter);
-
-
Aerial: they are attached to drones or aircrafts. Fast capture, but with less precision and high added cost.
There is no better or worse type of equipment. There is one that is best suited to your scope.
HOW DOES DATA PROCESSING WORK?
Basically, processing a point cloud consists of two steps:
-
Cleaning : during the scan, many objects that are in the surroundings are captured, but have no value to the project, such as pedestrians and cars. The points corresponding to these objects can be deleted from the point cloud, improving their visualization and decreasing the file size. Other unwanted points are also those called "noises", that is, points that do not exist, but are generated by reading errors. Mirrors, glass, polished or very dark surfaces produce a high degree of noise.
-
Registration: scanning consists of several scenes (captures) at different angles and / or environments. The process of joining these scenes into a single point cloud is called registration.

LS3D: COMO?
WHY USE 3D LASER SCAN?
And why not?
It is the most reliable and high quality measurement method at an affordable cost. It is already a reality in the world and in Brazil. In addition, ROI is very high due to the volume of benefits that its use brings.
REDUCES REWORK COSTS
REDUCES MANUAL MEASUREMENT ERRORS
REDUCES CHANGES TO PURCHASE CONTRACTS
REDUCES SCHEDULE DELAYS
REDUCES UNFORESEEN AND IMPROVISION
WHEN TO USE 3D LASER SCAN?

Whenever the measurement step is necessary.
NEW CONSTRUCTIONS
As built documentation
Documentary memory of the executed
Project compliance analysis
Quality measurement
RESTORATION, REFORMS AND ENLARGEMENTS
As is / As found documentation
Simulations of interventions
Quality measurement
Analysis and studies
WHY AND WHEN?
3D LASER SCANNING vs CONVENTIONAL TOPOGRAPHY
In most cases, these two methodologies are complementary , each with its function and application.
But what if it is necessary to choose?
First, it is important to understand your need.
Do a few points solve it?
Do you need georeferenced coordinates?
Will it have a single use?
Do you need the complete environment?
Without georeferencing?
Will it have several uses (studies, projects)?
Conventional topography
3D Laser Scanner
3D laser scanning captures a VOLUME OF INFORMATION that is not possible with any other method, including conventional topography.
So it is important that you understand your need . If there is a possibility to use the survey to increase the quality of your project or to reduce its uncertainties, scanning should be considered in your scope.
Both are accurate and affordable.
But, there is no way to compare the survey SPEED , the captured DATA VOLUME and the decision POWER you have with 3D laser scanning.

RICH
+
AGILE
LS3D vs TOPO
LASER SCANNER 3D + BUILDING INFORMATION MODELING | BIM
BIM is an intelligent project methodology that has as its main differentiator the attribution of information to the construction model.
Combining BIM with reality capture, we have a product with great POTENTIAL due to the immense range of POSSIBILITIES of studies, analyzes and projects that give greater POWER OF DECISION due to the volume of data and scenarios still in the planning phase.
POSSIBILITIES
CREATIVITY
POTENTIAL
DECISION POWER
EXECUTIVE PROJECT
CONCEPTUAL PROJECT
SURROUNDING STUDY
IMPACT STUDY
EXISTING STRUCTURES MODEL
SCENARIO SIMULATIONS
ANALYSIS
PATHOLOGIES, EFFICIENCY
APPLICATIONS
AT THE
LIFE CYCLE
ENERGY
VR / AR
REMODELING
AS IS / AS FOUND
OPERATION &
MAINTENANCE
PATHOLOGY
ASSET MANAGEMENT
DOCUMENTATION
DETAILS
PROJECT vs REAL
MANUFACTURING
MEASUREMENT OF
QUALITY
CONSTRUCTION
LOGISTICS
4D PLANNING
QUALITY ASSESSMENT
SITE LAYOUT
STUDY OF THE CRITICAL PATH
AS BUILT
LS3D + BIM
DRONE MAPPING
Aerial solution with photogrammetry

With photogrammetry technology, drone mapping captures all surfaces with photos and generates a 3D digital replica of the structure.
HOW?
The drone flight is planned and formatted to take pictures from various angles of the structure of interest. Then, these photos are aligned in specific software. At WRodacki, a 3D mesh of the structure is generated, which can be the final product. Or, the point cloud is created from the 3D mesh.
DRONE MAPPING vs 3D LASER SCANNER
Greater agility
Higher visual quality (color definition)
less precision
Lowest level of NP detail (resolution)
Legislative and airspace limitations
Limitations of shiny surfaces, water and site lighting
Less agility
Lower visual quality (color definition)
Higher precision
Higher level of detail (resolution)
Limitations of shiny surfaces, water and mirror
Drone mapping
3D Laser Scanner
VOCÊ SABIA?
Que para realizar medições de terras brasileiras é necessário o cadastro no Ministério da Defesa? As etapas são:
3D Laser Scanner
3D Laser Scanner
3D Laser Scanner
3D Laser Scanner
São analisados desde documentos de constituição da empresa até dados técnicos, como softwares e hardwares utilizados para realização dos serviços.
Nós da WRodacki possuímos conhecimento técnico reconhecido pelo Ministério da Defesa para a realização de aerolevantamento nas categorias A e B, ou seja, desde a coleta até o processamentos dos dados.
DRONE
bottom of page